Integrating AI into Advanced Process Control
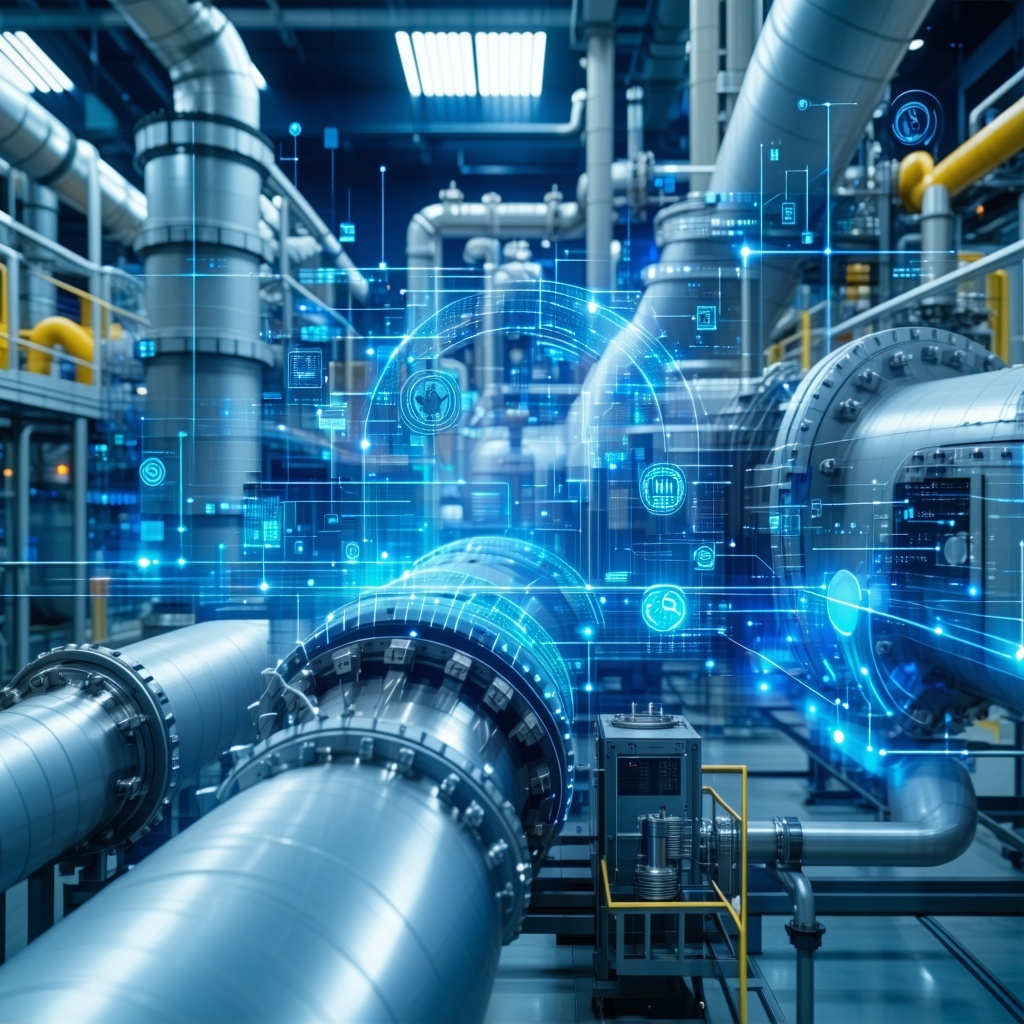
Introduction
Advanced Process Control (APC) has long been a key tool in process industries like oil refining, petrochemicals, and chemicals. It helps improve efficiency, reduce process variability, and push operations closer to optimal limits. APC systems often rely on strategies like Model Predictive Control (MPC), which use mathematical models to predict how a process behaves and decide the best control actions. However, as operations become more complex and dynamic—due to changes in raw materials, markets, and technology—traditional APC is no longer always enough. This is where Artificial Intelligence (AI), especially machine learning (ML), is starting to play a major role, adding flexibility, adaptability, and intelligence to control systems.
Challenges with Traditional APC
Traditional APC systems are excellent when they work with accurate, well-defined process models. But over time, real plant behavior can shift due to equipment wear, changes in raw materials, or evolving process conditions. This can lead to outdated or overly simplified models that affect control accuracy. Moreover, APC systems may struggle when faced with unexpected disturbances, non-linear behaviors, or when frequent manual retuning is required. AI helps address these issues by learning directly from data—both historical and real-time—allowing control systems to stay up-to-date and adjust automatically to changes in the plant.
Adaptive Model Updating
One major application of AI in APC is adaptive model updating. In traditional MPC, the control model is usually fixed and may need manual updates. With AI, models can now be updated automatically using techniques like neural networks or recursive regression. For example, at a large chemical plant in South Korea, an AI-based model continuously retrains itself on recent process data. This has reduced the need for frequent manual tuning and improved controller accuracy as the plant’s conditions change over time.
Soft Sensors
Another key application is the use of soft sensors. In many process plants, not all important variables can be measured directly or in real time. For instance, product composition, catalyst activity, or fouling levels often require lab testing or are measured infrequently. AI can be trained on historical data to act as a "virtual sensor" that estimates these hidden values in real time. A well-known refinery in Europe has implemented soft sensors using AI models to estimate naphtha quality during distillation. These predictions are fed into the APC system, enabling tighter control and higher product yield without waiting for lab results.
Anomaly Detection
AI is also improving how we detect problems in control performance. Traditional alarms may not always catch subtle issues until they grow into bigger problems. AI algorithms like autoencoders or clustering methods can analyze thousands of data points in real time, learn what normal behavior looks like, and flag early signs of anomalies. A U.S.-based LNG terminal has used AI for this purpose. Their AI system monitors process control loops and alerts operators to unusual patterns—like valve sticking or sensor drift—long before human operators or standard alarms would catch them.
Reinforcement Learning in APC
In more advanced settings, reinforcement learning (RL)—a type of AI where systems learn through trial and error—is being explored as an alternative control method. While this is still mostly in research or pilot stages, RL has shown promise in highly complex or non-linear systems. For instance, a global specialty chemicals company has run pilot tests where RL agents learn to control temperature in a batch reactor more efficiently than conventional methods. Over time, these RL-based controllers adapted to changing reaction kinetics, leading to better control and energy savings.
Integration with Existing APC Systems
Importantly, AI doesn’t have to replace existing APC systems. Instead, it adds a new intelligent layer that enhances them. A typical implementation might start by collecting historical and real-time data from distributed control systems (DCS) or data historians like AVEVA PI. AI models are trained on this data using tools like Python, MATLAB, or AspenTech’s AI Suite. Before deployment, they’re validated against digital simulations using tools such as UniSim or gPROMS to ensure safety and accuracy. Once ready, these models are integrated with existing APC platforms like Aspen DMC3 or Honeywell Profit Controller. Depending on infrastructure, they can run on local edge devices or on cloud servers, allowing scalability and remote monitoring.
A real-world example comes from a Middle East petrochemical plant, which integrated machine learning into its APC for a polymer reactor. Using real-time data, the AI model predicted polymer quality more accurately than the lab-based delay measurements. This allowed operators to adjust feeds and temperatures proactively, improving product consistency and reducing waste.
Conclusion
In conclusion, AI is not here to replace APC, but to transform it. By combining the predictive power of machine learning with traditional control systems, we are entering a new era of "autonomous APC". These systems are smarter, continuously learning, and can adjust in real time without human intervention. Plants that adopt AI-enhanced APC can operate more efficiently, respond faster to changes, reduce downtime, and stay competitive in a rapidly digitalizing world. With AI, the future of process control is adaptive, predictive, and truly intelligent.
Digital Manufacturing Operations (DMO)
Digital Manufacturing Operations (DMO) is Tridiagonal’s offering that drives intelligent, connected, and efficient manufacturing. Acting as the nerve center of smart operations, DMO enables real-time decisions and streamlined workflows across the value chain.
Book A Meeting →Domain-Wise PlantGPT
It is built around purpose-designed micro-agents that collaborate to provide real-time conversational assistance, decision support, and advisory insights tailored to daily plant operations.
Book A Demo →Dx. Consulting Services
Our strength lies in the fusion of deep consulting experience, process domain expertise, and digital execution excellence. This rare combination enables us to go beyond traditional digital transformation.
Book A Meeting →FAQ
It has survived not only five centuries, but also the leap into electronic.
Life Science / Pharma
reproduced below for those interested. Sections 1.10.32 and 1.10.33 from "de Finibus Bonorum et Malorum" by Cicero are also reproduced in their exact original form, accompanied by English versions.
There are many variations of passages of Lorem Ipsum available, but the majority have suffered alteration in some form.
Life Science / Pharma
reproduced below for those interested. Sections 1.10.32 and 1.10.33 from "de Finibus Bonorum et Malorum" by Cicero are also reproduced in their exact original form, accompanied by English versions.
There are many variations of passages of Lorem Ipsum available, but the majority have suffered alteration in some form.
Life Science / Pharma
reproduced below for those interested. Sections 1.10.32 and 1.10.33 from "de Finibus Bonorum et Malorum" by Cicero are also reproduced in their exact original form, accompanied by English versions.
There are many variations of passages of Lorem Ipsum available, but the majority have suffered alteration in some form.
Life Science / Pharma
reproduced below for those interested. Sections 1.10.32 and 1.10.33 from "de Finibus Bonorum et Malorum" by Cicero are also reproduced in their exact original form, accompanied by English versions.
There are many variations of passages of Lorem Ipsum available, but the majority have suffered alteration in some form.
Life Science / Pharma
reproduced below for those interested. Sections 1.10.32 and 1.10.33 from "de Finibus Bonorum et Malorum" by Cicero are also reproduced in their exact original form, accompanied by English versions.
There are many variations of passages of Lorem Ipsum available, but the majority have suffered alteration in some form.
Life Science / Pharma
reproduced below for those interested. Sections 1.10.32 and 1.10.33 from "de Finibus Bonorum et Malorum" by Cicero are also reproduced in their exact original form, accompanied by English versions.
There are many variations of passages of Lorem Ipsum available, but the majority have suffered alteration in some form.
Related Blogs
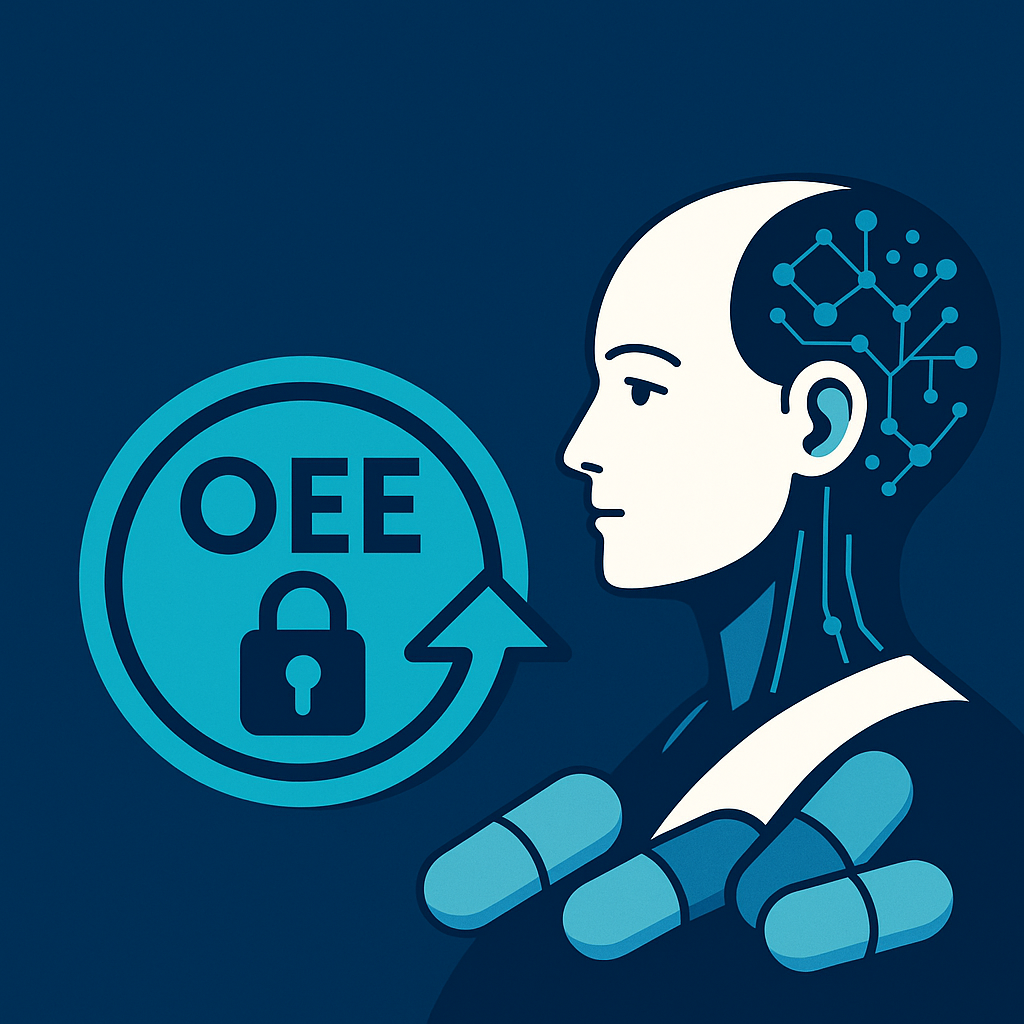
Smarter OEE: Unlocking Pharma Efficiency with Agentic AI
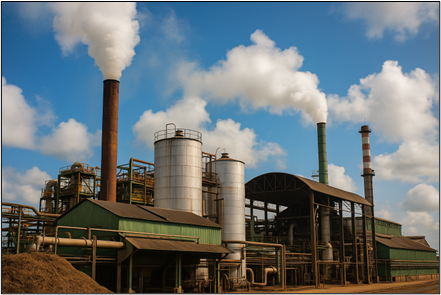
Forecasting Failures: Smart Maintenance of Falling Film Evaporators in the Sugar Manufacturing industry
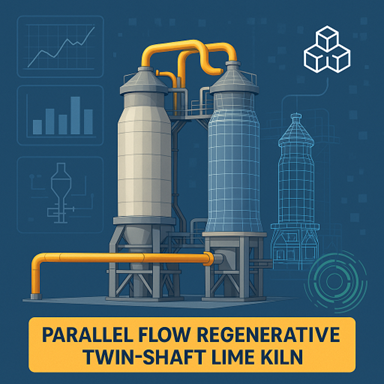