AI & ML in Oil and Gas Operations Management
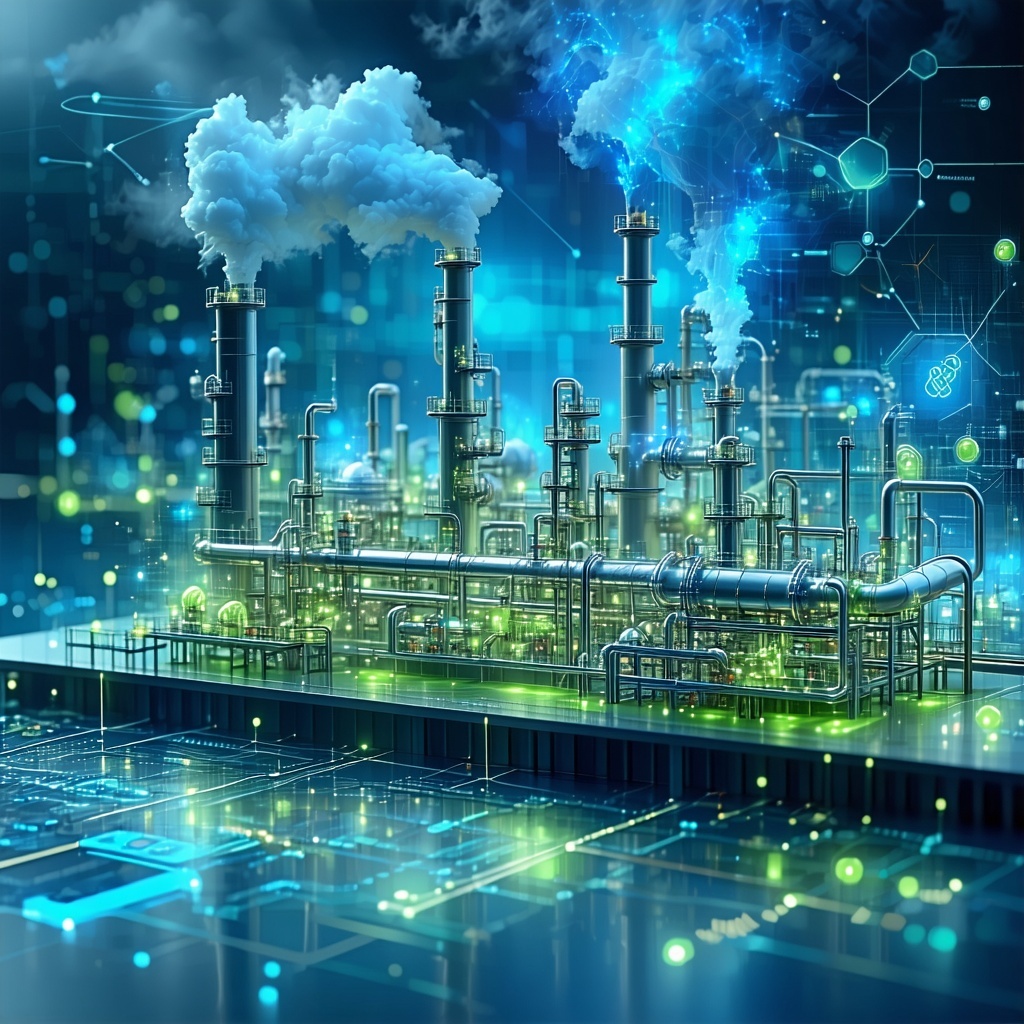
Introduction
Oil and gas plant extension projects, whether involving the addition of a new compressor train, revamp of an aging utility unit, or integration of advanced separation equipment, are among the most intricate, high-pressure undertakings in the energy sector. Though often backed by detailed schedules, technical specs, and engineering designs, these projects almost always suffer from one persistent truth: reality rarely follows the plan. Delays emerge not because of a lack of knowledge or tools, but due to the inherent complexity of managing multiple moving parts, work fronts, vendors, safety protocols, shifting scopes, and volatile resource availability all under strict budget and deadline constraints.
The Complex Reality of Oil and Gas Plant Extension Projects
One of the most pervasive issues is resource levelling failure. Despite having thousands of work hours scheduled, the actual allocation of manpower, cranes, scaffolding, and inspection crews often results in crowding at one area while another lies idle. Teams clash over work fronts, safety zones are compromised, and productivity drops, leading to cascading delays. Compounding this are issues of unclear accountability and scope overlap. When mechanical contractors believe they’re responsible for equipment alignment but commissioning engineers disagree, or when cable laying overlaps with scaffolding takedown, confusion leads to idle time, duplicated work, and change orders that inflate cost and strain timelines.
Resource Levelling Failures: A Core Field-Level Breakdown
One of the most frequent field-level inefficiencies is poor resource levelling. Projects may have thousands of manhours scheduled, yet actual resource deployment often results in:
- Overcrowding in some areas while other zones remain idle.
- Inter-team clashes over limited work fronts and safety boundaries.
- Compromised safety and reduced productivity.
Beyond these field-level inefficiencies lies a larger, more systemic problem: fragmented and delayed information flow. Traditional project management tools Gantt charts, critical path analysis, and milestone trackers, are useful at the planning stage but are not built for dynamic decision-making once execution starts. Updates come in through scattered channels: email threads, paper checklists, supervisor WhatsApp groups, or manually edited Excel sheets.
Critical decisions, such as whether to proceed with hydrotesting despite pending support welding, often rely on gut instinct rather than live data. Worse still, by the time a project manager realises that CPI has dropped below 0.8 or SPI dipped under 0.9, the impact has already been felt on site. These are Earned Value Management (EVM) Indicators—Cost Performance Index (CPI) and Schedule Performance Index (SPI) are reactive, not predictive. They confirm that the project is off-track but don’t offer insight into why it’s happening or how to fix it quickly. As a result, firefighting is the norm with planners rescheduling tasks daily, procurement scrambling to expedite missing materials, and site teams pushing work through at the cost of quality or safety.
To address these deeply embedded challenges, forward-thinking project leaders are turning to data-centric and AI-enhanced systems that transform execution into a smarter, more predictive process. The cornerstone of this transformation is the adoption of data lakes, centralised repositories that ingest all types of project data in real-time.
This often leads to cascading delays, as one delay triggers a domino effect across dependent activities. For example, crane availability or scaffolding access may become a bottleneck not because of scarcity, but because of poor scheduling and visibility across teams.
These aren’t just digital filing cabinets for reports; they house structured information (task schedules, BOMs, WBS), semi-structured content (Excel sheets, inspection logs), and unstructured data (PDFs, photos, sensor feeds, emails). Feeding into this, a data warehouse organises and cleans the most critical operational data, transforming it into actionable dashboards that update automatically. This visibility allows project teams and decision-makers to monitor evolving KPIs—manpower efficiency, contractor performance, task sequencing risks, material lead times, and respond in real-time. Imagine a dashboard that doesn’t just show that piping completion is delayed, but pinpoints that crew performance dropped after scaffolding was reassigned, while valve deliveries are stuck in customs, potentially impacting mechanical completion dates.
Scope Ambiguity and Accountability Gaps
The connected intelligence enables decisions backed by data, not guesswork. Furthermore, machine learning (ML) models trained on historical project data can identify risk patterns far earlier than human intuition. They learn that whenever cable tray fabrication is delayed by more than a week, associated electrical completion slips by at least two weeks. They warn that if civil handover to mechanical exceeds a certain threshold, the project’s commissioning timeline is compromised. These insights allow for proactive replanning, not last-minute scrambling. Even more powerful is the application of Large Language Models (LLMs). These models can process dense technical documents, scopes of work, contract clauses, method statements, and convert them into structured, task-specific summaries. They eliminate ambiguity in responsibilities, ensure that teams are aligned, and even draft reports, delay notices, and technical justifications automatically, saving hours of administrative overhead.
At the budgeting level, AI tools help ensure tighter cost control. When a subcontractor submits a bill claiming 90% completion of an activity, the system can verify this claim against actual progress data from site logs, IoT sensors, inspection reports, and WBS alignment. This prevents overbilling, reduces disputes, and ensures that payment is aligned with performance. Financial controllers can also compare committed, accrued, and actual costs in real time, enabling better cash flow forecasting and tighter capital discipline. Procurement teams benefit too: when material delivery delays start affecting critical path activities, the system doesn’t just flag a red status, it recommends which task sequence can be rescheduled without impacting commissioning, or whether float from a non-critical system can be borrowed. These AI-backed suggestions go far beyond static Gantt chart logic; they are rooted in live project conditions.
Moreover, when integrated with real-time field data such as sensor inputs from installed equipment, drone footage of progress, and site access logs, AI models can provide a live view of workforce readiness. They can detect work fronts that are resource-heavy but stagnant, identify weather or permit-related disruptions early, and flag deviations between planned and actual quantities. This real-time feedback loop converts project controls from a reporting function into a strategic driver of execution. The future is even more promising: with federated learning, companies will be able to securely pool anonymised project data across organisations, training even smarter models for cost estimation, risk prediction, and contractor benchmarking without compromising data privacy.
Conclusion
To summarise, oil and gas plant extension projects are no longer suffering from a lack of effort or tools they are challenged by information silos, reactive decision-making, and a lack of predictive control. By integrating traditional project management principles with advanced, AI-driven analytics and unified data platforms, teams can finally gain the visibility, speed, and accuracy needed to deliver complex projects on time and within budget. Data lakes eliminate the chaos of disconnected inputs, ML turns past failures into future foresight, and LLMs convert document overload into clarity and communication. It’s time for project management to evolve from control-by-reports to execution-by-intelligence. Those who adopt this shift will find not only improved cost and schedule performance but also a far more resilient, informed, and agile project culture.
Digital Manufacturing Operations (DMO)
Digital Manufacturing Operations (DMO) is Tridiagonal’s offering that drives intelligent, connected, and efficient manufacturing. Acting as the nerve center of smart operations, DMO enables real-time decisions and streamlined workflows across the value chain.
Book A Meeting →Domain-Wise PlantGPT
It is built around purpose-designed micro-agents that collaborate to provide real-time conversational assistance, decision support, and advisory insights tailored to daily plant operations.
Book A Demo →Dx. Consulting Services
Our strength lies in the fusion of deep consulting experience, process domain expertise, and digital execution excellence. This rare combination enables us to go beyond traditional digital transformation.
Book A Meeting →FAQ
It has survived not only five centuries, but also the leap into electronic.
Life Science / Pharma
reproduced below for those interested. Sections 1.10.32 and 1.10.33 from "de Finibus Bonorum et Malorum" by Cicero are also reproduced in their exact original form, accompanied by English versions.
There are many variations of passages of Lorem Ipsum available, but the majority have suffered alteration in some form.
Life Science / Pharma
reproduced below for those interested. Sections 1.10.32 and 1.10.33 from "de Finibus Bonorum et Malorum" by Cicero are also reproduced in their exact original form, accompanied by English versions.
There are many variations of passages of Lorem Ipsum available, but the majority have suffered alteration in some form.
Life Science / Pharma
reproduced below for those interested. Sections 1.10.32 and 1.10.33 from "de Finibus Bonorum et Malorum" by Cicero are also reproduced in their exact original form, accompanied by English versions.
There are many variations of passages of Lorem Ipsum available, but the majority have suffered alteration in some form.
Life Science / Pharma
reproduced below for those interested. Sections 1.10.32 and 1.10.33 from "de Finibus Bonorum et Malorum" by Cicero are also reproduced in their exact original form, accompanied by English versions.
There are many variations of passages of Lorem Ipsum available, but the majority have suffered alteration in some form.
Life Science / Pharma
reproduced below for those interested. Sections 1.10.32 and 1.10.33 from "de Finibus Bonorum et Malorum" by Cicero are also reproduced in their exact original form, accompanied by English versions.
There are many variations of passages of Lorem Ipsum available, but the majority have suffered alteration in some form.
Life Science / Pharma
reproduced below for those interested. Sections 1.10.32 and 1.10.33 from "de Finibus Bonorum et Malorum" by Cicero are also reproduced in their exact original form, accompanied by English versions.
There are many variations of passages of Lorem Ipsum available, but the majority have suffered alteration in some form.
Related Blogs
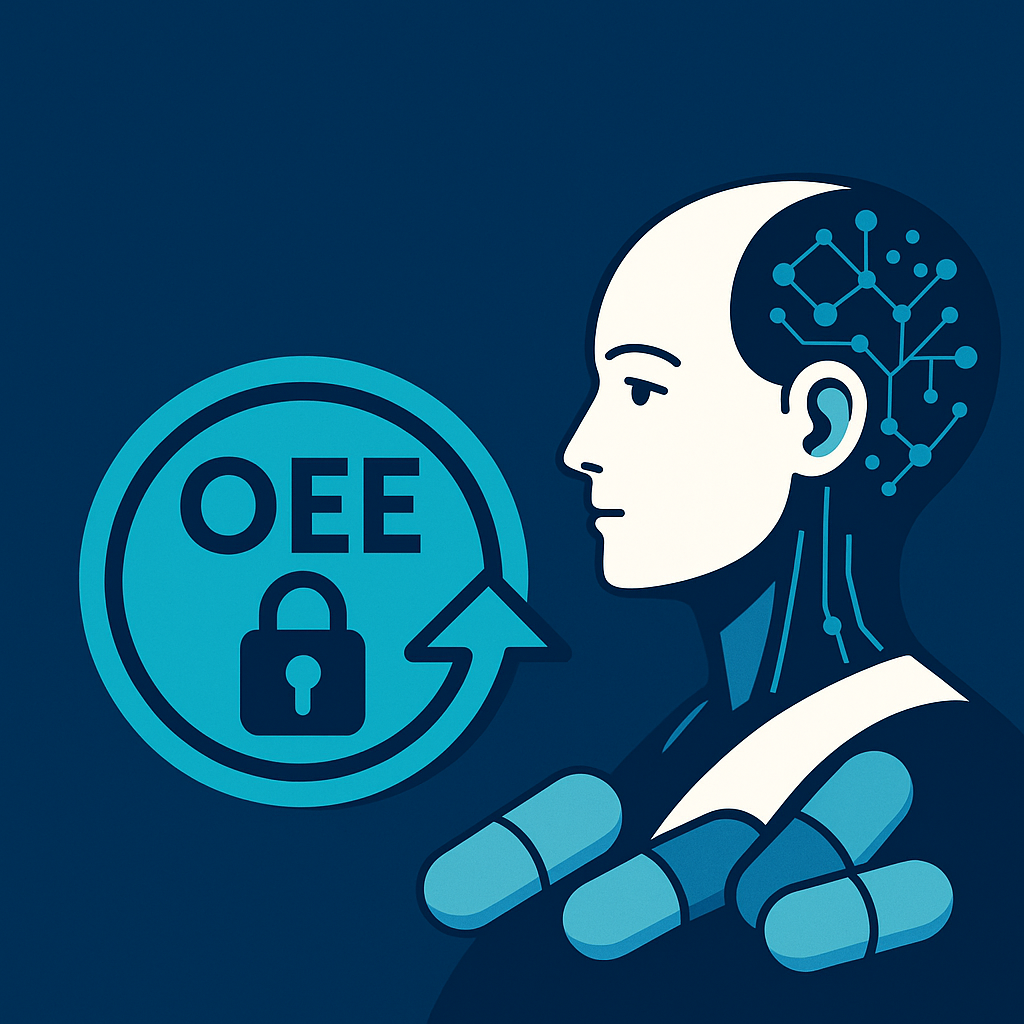
Smarter OEE: Unlocking Pharma Efficiency with Agentic AI
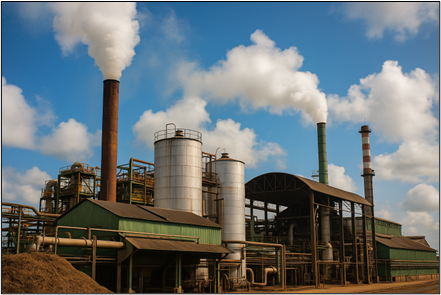
Forecasting Failures: Smart Maintenance of Falling Film Evaporators in the Sugar Manufacturing industry
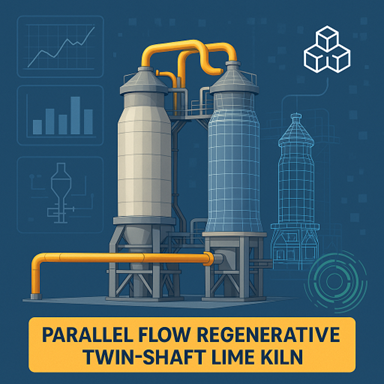